Knowledge Modules for Battery Cells “Made in Germany”
The production of battery cells includes many consecutive process steps. There is mixing, stirring, coating, rolling, cutting and stacking. Scientists at ProZell work to improve the quality of the final product, make production more cost-effective and environmentally friendly. The competence cluster for battery cell production, in which MEET Battery Research Center of University of Münster and Helmholtz Institute Münster (HI MS) of Forschungszentrum Jülich participate, is supported by the German Federal Ministry of Education and Research (BMBF). To transfer research results into industrial application quickly ProZell encourages knowledge transfer into industry. This year the third edition of ProZell industry day was held in a digital conference format on 27 October 2020.
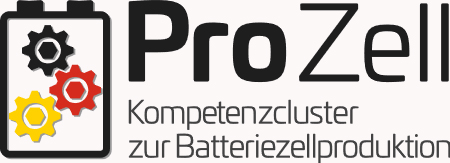
“With our research at ProZell we want to contribute to the BMBF roof concept ‘Battery ResearchFactory’ and establish an industrial serial production of battery cells in Germany and Europe which is internationally competitive”, says Professor Arno Kwade, speaker of the competence cluster ProZell and Director of the Institute for Particle Techology of TU Braunschweig. “Today we demonstrate what is successfully possible on a laboratory and pilot scale. Now the learned needs to be transferred into industrial use.”
By organising an industry day the cluster promotes dialogue between the involved participants from industry and academia. Further, cooperation were established, industrial as well as scientific demands were identified and research results were presented. It was shown, for example, how thicker electrodes increase the energy density in battery cells. Single production processes can be accelerated and lead to a decrease in costs. Furthermore, new process technologies for electrode production were presented that use less or no solvents, save material costs and thus improve the ecological footprint.
Research along the Value Cycle
“MEET and HI MS contribute various projects to the competence cluster", explains Prof. Dr. Martin Winter, Scientific Leader of MEET Battery Research Center at University of Münster and Helmholtz Institute Münster of Forschungszentrum Jülich. "With our interdisciplinary, application-oriented and holistic research, our scientists contribute to ProZell along the entire value-added cycle of battery cells," says Winter.
In ProZell, MEET and HI MS researchers are working on the following projects:
- Optimized electrode structure and density by integrated design of blending and calendering processes
- Process-structure-characteristics relationship for filling and wetting processes of large-size lithium-ion batteries (Cell-Fill)
- Innovative recycling processes for new lithium cell generations (InnoRec)
- Pre-lithiation of electrodes (PräLi)
Competence cluster ProZell
In cooperation with BMBF, the competence network for lithium-ion batteries (KLiB) and the ProZell management circle, the vivid ProZell network creates successful synergies between science and industry. ProZell aims at establishing the foundations for a powerful and cost-effective battery cell production “Made in Germany”. Partners of the network are TU Braunschweig, Karlsruhe Institute of Technology, Hochschule Landshut, TU Berlin, TU Clausthal, TU Freiberg, ZSW Baden-Württemberg, German Aerospace Center via Helmholtz Institute Ulm, University of Ulm, RWTH Aachen, TU Dresden, TU München, University of Münster via MEET Battery Research Center Münster, Fraunhofer-Gesellschaft and Forschungszentrum Jülich via Helmholtz Institute Münster.